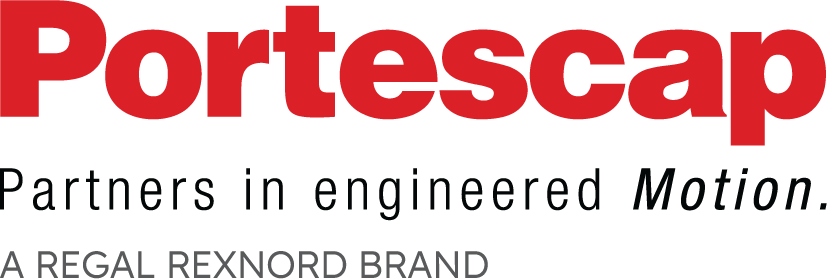
Keeping the temperature down: thermal management techniques for miniature DC motors
Daniel Muller, Application Engineer at Portescap, explains the thermal management considerations your miniature motor manufacturer should make.
Excess internal temperature will damage a motor and its components. Even before it gets to that stage, thermal management impacts performance, not least by power conversion efficiency. When developing a miniature motor, it’s vital to ensure that the design and materials used minimise losses to heat, as well as improve the motor’s heat dissipation ability.
A coreless brush DC motor is typically designed as a self-supporting coil rotating in the airgap between a permanent magnet and housing, which are both part of the stator. As the coil temperature rises, the heat transfers from the coil to the tube and then from the tube to the ambient environment. As electrical current flows through the coil, its temperature rises, heat dissipation begins and increases to a point where it exactly compensates the heat generation. At this point, thermal energy contained in the motor is constant over time.
Brushless motors use the same working principle as brushed motors except that the coil is fixed in the stator and the permanent magnet is rotating with the shaft. The moving magnetic field around the stator results in iron losses, where an electrical current is induced within the iron laminations of the stator. This current generates heat, adding to the heat already generated in the coil. Iron losses are proportional to motor speed; they aren’t significant at lower speed but become greater at high speed and at this stage, torque must be reduced.
Whether brush or brushless technology is required, the thermal challenge is the same: keep the coil temperature below its maximum, admissible temperature. Creating a contact of high thermal conductivity with the motor can improve heat dissipation. This can be achieved by increasing the surface exchanging heat with the ambient air, for example. In most cases, a motor installed on a metallic base, mounted from its front face onto a metal stand that will help drain heat out of the motor, provides better cooling than having the motor surrounded by air only.
Motor designers and manufacturers like Portescap engage with customers early in their development process to assess the dissipation capability of a motor or motor/gearbox assembly. Taking the specific application setting into account, the design and configuration can then be optimised for best motor performance.
Some applications require high torque for a short duration. Industrial power tools, such as screwdrivers, require speed during the run-down phase and then peak torque during the tightening phase, which typically lasts up to a second. For a peak torque requirement, a motor can be supplied with a current that exceeds the motor’s maximum rated continuous current as long as the coil temperature doesn’t exceed its maximum admissible temperature. This means that the duration of the operation must be limited.
Slotless brushless motors are particularly well-suited for short peak torque as the design makes it possible to typically reach 10 times the motor’s maximum continuous torque with 10 times higher current. At the same time, slotless coil designs can accumulate a great quantity of thermal energy thanks to their higher thermal capacity, making it possible to provide high torque during a short duration without relying on heat dissipation.
Another way to manage heat to improve motor performance is to design stators with an integrated air path so that the air flow can carry heat away from the motor. This focuses on the heat convection inside the motor, rather than designs that rely mainly on heat conduction. It might also be possible to integrate a fan on the motor shaft, driving airflow through the motor body as it is operating.
The lifetime and performance of a miniature motor is closely linked to successful heat management. The solution depends on the challenges of each individual application setting and the success factors required, be that achieving a given torque to realising maximum efficiency. To design a system most capable of achieving your specific mini motor application goals, the input of an experienced design team is valuable for success.
Image 1: To optimise performance and efficiency motor manufacturers have to design the right thermal management solution according to the application requirements.
Image 2: Slotless coil designs can accumulate a great quantity of thermal energy thanks to their higher thermal capacity, making it possible to provide high torque during a short duration without relying on heat dissipation.
Image 3: Water Analogy of Heat Transfer in a Motor.
Image 4: Coil temperature stabilizes at a given temperature when the current is constant over time.
Portescap offers the broadest miniature and specialty motor products in the industry, encompassing coreless brush DC, brushless DC, stepper can stack, gearheads, digital linear actuators, and disc magnet technologies. Portescap products have been serving diverse motion control needs in wide spectrum of medical and industrial applications, lifescience, instrumentation, automation, aerospace and commercial applications, for more than 70 years.
Portescap has manufacturing centers in the United States and India, and utilizes a global product development network with research and development centers in the United States, China, India and Switzerland.
For more information, visit www.portescap.com
Tel: +44 (0)1905 917477
Web: news.dmaeuropa.com
Email: press-team@dmaeuropa.com
Address: Progress House, Midland Road, Worcester, Worcestershire, WR5 1AQ, United Kingdom
Reader Contact:Portescap: Nicole Monaco
Tel: +1 404.877.2534
Email: sales.europe@portescap.com